How does the Induction Sealing Process Work?
To begin sealing, the container must first pass under the induction sealing coil, where the induction heating process takes place. Induction heating is a phenomenon where electrical energy is transferred to a conductive material, such as foil, by means of an electromagnetic field.
When the container moves under the coil, the induction coil generates an electromagnetic field that induces eddy currents in the aluminum foil liner of the container's cap. These eddy currents generate heat through electrical resistance and cause the foil to heat up. As the foil heats up, the wax layer of the liner melts and bond the foil to the container's opening. As this happens, the cardboard backing of the liner separates and remains on the inside of the cap. As the container exits the induction sealer and the heat seal cools, the foil firmly adheres to the container opening, creating a strong, reliable seal.
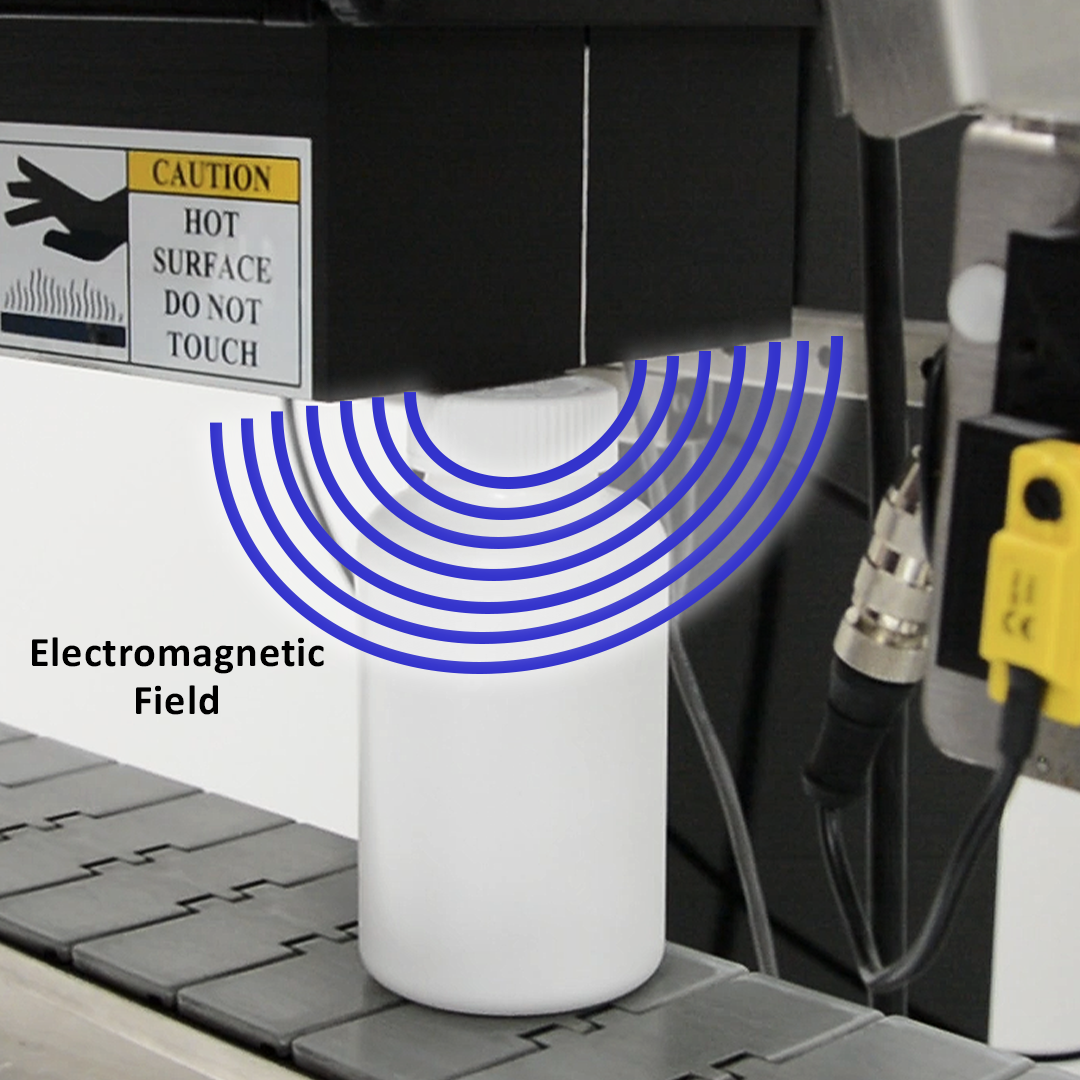